Hot wire CNC
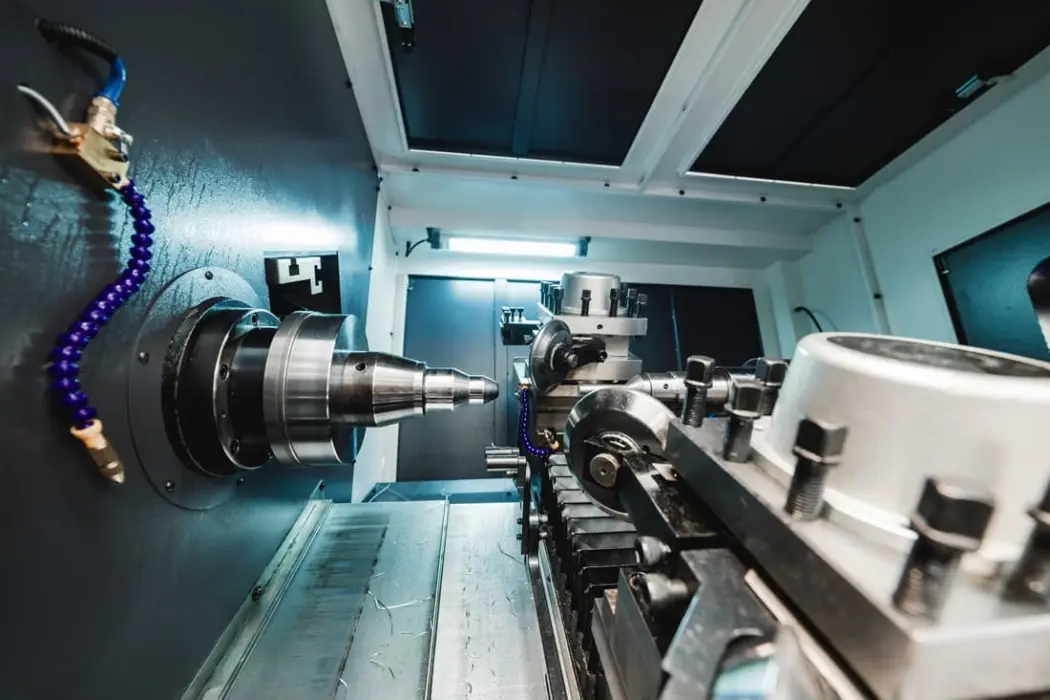
Welcome to our comprehensive article on the cutting-edge technology of Hot Wire CNC! In this piece, we will delve into the inner workings of this innovative machinery and explore its numerous advantages. From unmatched precision and efficiency to its wide range of applications in various industries, including architecture and aerospace, Hot Wire CNC has revolutionized the way we approach cutting tasks.
If you’re considering investing in a Hot Wire CNC machine, we’ve got you covered too. We’ll guide you through the factors to consider when choosing the right machine for your needs. Additionally, we’ll provide a comparative analysis between hot wire CNC and traditional cutting methods, highlighting the unique benefits that this advanced technology brings to the table.
But that’s not all we’ll also take a glimpse into the future prospects of Hot Wire CNC. With constant innovations and advancements in the field, there is no doubt that this technology holds immense potential for further growth and development.
So sit back, relax, and join us on this exciting journey as we unravel the mysteries behind Hot Wire CNC. Whether you’re an industry professional or simply curious about cutting-edge technologies, this article aims to create a sense of connection and rapport with you as we explore every aspect of this fascinating subject. Let’s dive in!
How Does Hot Wire CNC Work? Exploring the Cutting-edge Technology
The hot wire CNC, or Computer Numerical Control, is a cutting-edge technology that operates on the principle of thermal cutting. It uses a heated wire to cut through materials like foam and plastic with extreme precision. The process begins when an electric current passes through a thin wire, heating it to temperatures high enough to melt or vaporize the material being cut. This wire is controlled by a computer program which guides it along predetermined paths, allowing for intricate designs and patterns to be created.
One of the key aspects of hot wire CNC technology is its ability to produce clean cuts without leaving any debris behind. This is because the heat from the wire instantly melts the material around it, leaving no room for dust or particles to form. Furthermore, since there’s no physical contact between the tool and the material apart from where the cutting takes place, there’s minimal wear on the tool itself. This not only extends its lifespan but also reduces maintenance costs significantly.
Another noteworthy feature of hot wire CNC machines is their versatility in handling different types of materials and shapes. Whether you’re working with rigid foam for architectural models or flexible foam for packaging purposes, this machine can deliver precise cuts every time. Moreover, it can handle complex 3D shapes with ease thanks to its multi-axis movement capability. By inputting your design into the computer software, you can guide the machine to move in any direction - horizontally, vertically or diagonally - ensuring that every cut is exactly as per your specifications.
Advantages of Hot Wire CNC: Unmatched Precision and Efficiency
One of the most significant advantages of hot wire CNC technology is its unmatched precision. This cutting-edge technology allows for intricate designs to be cut with an accuracy that traditional methods simply cannot match. The hot wire, guided by computer numerical control (CNC), can follow complex paths and create detailed shapes with minimal error. This level of precision is particularly beneficial in industries where even the smallest discrepancy can have significant consequences, such as aerospace or medical device manufacturing.
Another key advantage of hot wire CNC machines is their efficiency. Unlike other cutting methods that may require multiple passes or stages to achieve the desired result, a hot wire CNC machine can often complete the task in a single pass. This not only speeds up production times but also reduces waste, as there’s less chance of material being damaged or incorrectly cut. Furthermore, because the process is automated, it requires less manual labor and can operate continuously without breaks, further increasing productivity.
The combination of precision and efficiency offered by hot wire CNC technology translates into cost savings for businesses. With faster production times and less waste, companies can reduce their operating costs and increase their profit margins. Additionally, the high-quality results produced by these machines can lead to increased customer satisfaction and repeat business. In an increasingly competitive market environment, these benefits make hot wire CNC an attractive option for many manufacturers.
Applications of Hot Wire CNC in Various Industries: From Architecture to Aerospace
The versatility of Hot Wire CNC technology has led to its widespread application across a variety of industries. In the field of architecture, for instance, this cutting-edge technology is used to create intricate models and prototypes with unmatched precision. The ability to cut complex shapes from foam or other materials quickly and accurately makes it an invaluable tool for architects and designers. Moreover, the efficiency of Hot Wire CNC reduces waste material, making it a more sustainable choice.
Moving on to the aerospace industry, Hot Wire CNC machines play a crucial role in manufacturing components with complex geometries. These machines are capable of producing parts with high dimensional accuracy which is paramount in aerospace applications where even the slightest deviation can lead to catastrophic results. Furthermore, the speed at which these machines operate significantly reduces production time, thereby increasing overall productivity.
But the applications of Hot Wire CNC are not limited to just architecture and aerospace. Other industries such as automotive, marine, and even arts and crafts have found uses for this innovative technology. Whether it’s creating custom car parts or crafting intricate sculptures, the precision and efficiency offered by Hot Wire CNC make it an indispensable tool in any industry that requires detailed cutting work. As we continue to explore its potential uses, there’s no doubt that this technology will continue to revolutionize how we design and manufacture products.
Choosing the Right Hot Wire CNC Machine: Factors to Consider
When it comes to choosing the right hot wire CNC machine, there are several factors that you need to consider. The first and foremost is the size of your project. If you’re working on a large-scale project, you’ll need a machine with a larger cutting area. On the other hand, if your projects are typically smaller in scale, a compact machine may be more suitable. Additionally, consider the type of material you will be cutting. Different machines are designed to handle different materials, so ensure that the one you choose can effectively cut your chosen material.
The second factor to consider is the precision level required for your projects. Hot wire CNC machines offer unmatched precision and efficiency, but not all machines are created equal. Some offer higher levels of precision than others. Therefore, if your work requires high levels of accuracy, opt for a machine known for its precise cuts. Furthermore, take into account the speed at which the machine operates. A faster operating speed can significantly reduce production time and increase efficiency.
Lastly, don’t overlook the importance of software compatibility when choosing a hot wire CNC machine. The software controls how the machine operates and plays an integral role in achieving desired results. Ensure that the software is user-friendly and compatible with your current systems to avoid potential operational issues down the line. Also consider after-sales service and technical support offered by manufacturers as these can greatly influence user experience especially during troubleshooting or maintenance periods.
Hot Wire CNC vs. Traditional Cutting Methods: A Comparative Analysis
When comparing hot wire CNC to traditional cutting methods, several key differences emerge. Traditional cutting methods, such as manual or mechanical sawing, grinding, and milling, have been the industry standard for many years. However, these methods often require significant time and effort, and can result in material waste due to inaccuracies. On the other hand, hot wire CNC technology offers a high degree of precision that significantly reduces waste while increasing efficiency.
The use of computer numerical control (CNC) in hot wire cutting allows for intricate designs to be executed with unparalleled accuracy. This is a stark contrast to traditional methods which are limited by human error and the physical constraints of manual tools. Furthermore, hot wire CNC machines can operate continuously without fatigue, unlike human operators. This not only increases productivity but also ensures consistent quality throughout the production process.
Another notable advantage of hot wire CNC over traditional cutting methods is its versatility across various materials. While traditional methods may struggle or be unsuitable for certain materials like foam or delicate plastics, hot wire CNC cuts through them with ease while maintaining a clean edge finish. This makes it an ideal choice for industries requiring precise cuts on diverse materials. Despite these advantages, it’s important to note that initial setup costs for hot wire CNC machines may be higher than those for traditional equipment. However, considering their benefits in terms of precision, efficiency and versatility, they represent a worthwhile investment for businesses looking to stay competitive in today’s fast-paced industrial landscape.
Future Prospects of Hot Wire CNC: Innovations and Advancements in the Field
As we look towards the future, the prospects of hot wire CNC technology are incredibly promising. The industry is continuously innovating, with advancements in precision, speed, and versatility leading the way. These improvements are largely driven by the increasing demand for more efficient and accurate cutting methods across various sectors. From aerospace to architecture, industries are recognizing the unmatched capabilities of hot wire CNC machines and investing heavily in this cutting-edge technology.
One significant area of advancement is in software development for hot wire CNC machines. Newer software versions offer enhanced control over cutting parameters, allowing for even greater precision and efficiency. Additionally, advancements in machine learning and artificial intelligence have opened up possibilities for automated adjustments during the cutting process. This not only reduces human error but also significantly increases productivity by minimizing downtime.
Furthermore, research is underway to explore how hot wire CNC technology can be integrated with other manufacturing processes for a more streamlined production workflow. For instance, combining it with 3D printing could potentially revolutionize how complex structures are created. As these innovations continue to unfold, it’s clear that hot wire CNC technology will play an increasingly vital role in shaping our future industries. Therefore, investing time and resources into understanding and utilizing this technology could prove invaluable for businesses looking to stay ahead of the curve.
Autor: Materiał partnera